
Installation method
As a reminder, it is possible to drive sheet piles into any type of soil (except rock). The choice of the installation method and of the pile driving equipment shall consider the whole system as mentioned above. Additionally, a piling job can only be successful if it is based on an extensive soil investigation. Note that in European Nordic countries, when a rock layer is quite shallow and the embedded depth of the sheet pile is not sufficient to activate the required passive resistance of the soil, rock-bolting is a quite common method to pin the sheet pile toe at the rock level (see our brochure Rockbolts).
The installation of an HZ-M/AZ combined wall system (with king piles and infill sheets) requires a specific installation sequence. A suitable rigid template with two levels guiding frame is mandatory unless you use a vibratory hammer / impact hammer fixed on a leader with an additional template!
Besides, the execution of circular cells is quite special topic. For details on these specific installation techniques, see our Piling Handbook, our AS 500 brochure, and watch the video animations on our YouTube channel (click here).
Standard installation techniques use vibratory hammers, impact hammers or presses, or a combination of these driving equipment. For instance, in compact soils layers, it might be faster and more efficient to start driving long sheet piles with a vibratory hammer or pressing machine, and then finish the last meters with an impact hammer.
Standard installation methods are
- panel driving,
- panel driving combined with staggered driving,
- pitch and drive,
- ...
In some specific soils, it is recommended to prevent clogging of the interlocks. This can be achieved by applying inside the interlocks a foam, a bituminous product (sealing system), or welding a plate / screw at the bottom of the interlock.
Panel driving
This method consists in erecting a panel inside a stiff template (preferably a two level template) before driving the sheet piles. Usually, each element of the panel is driven a few meters into the ground in a specific sequence. It is recommended- for permanent walls (i.e. underground car parks, basements),
- when installation tolerances are quite important (i.e. interlocks with a sealing system),
- in soils where leaning is predicted (i.e. in very soft soils)
- ...
Main disadvantage: this procedure takes more time (handling & threading the piles), needs longer crane boom (lifting of piles).
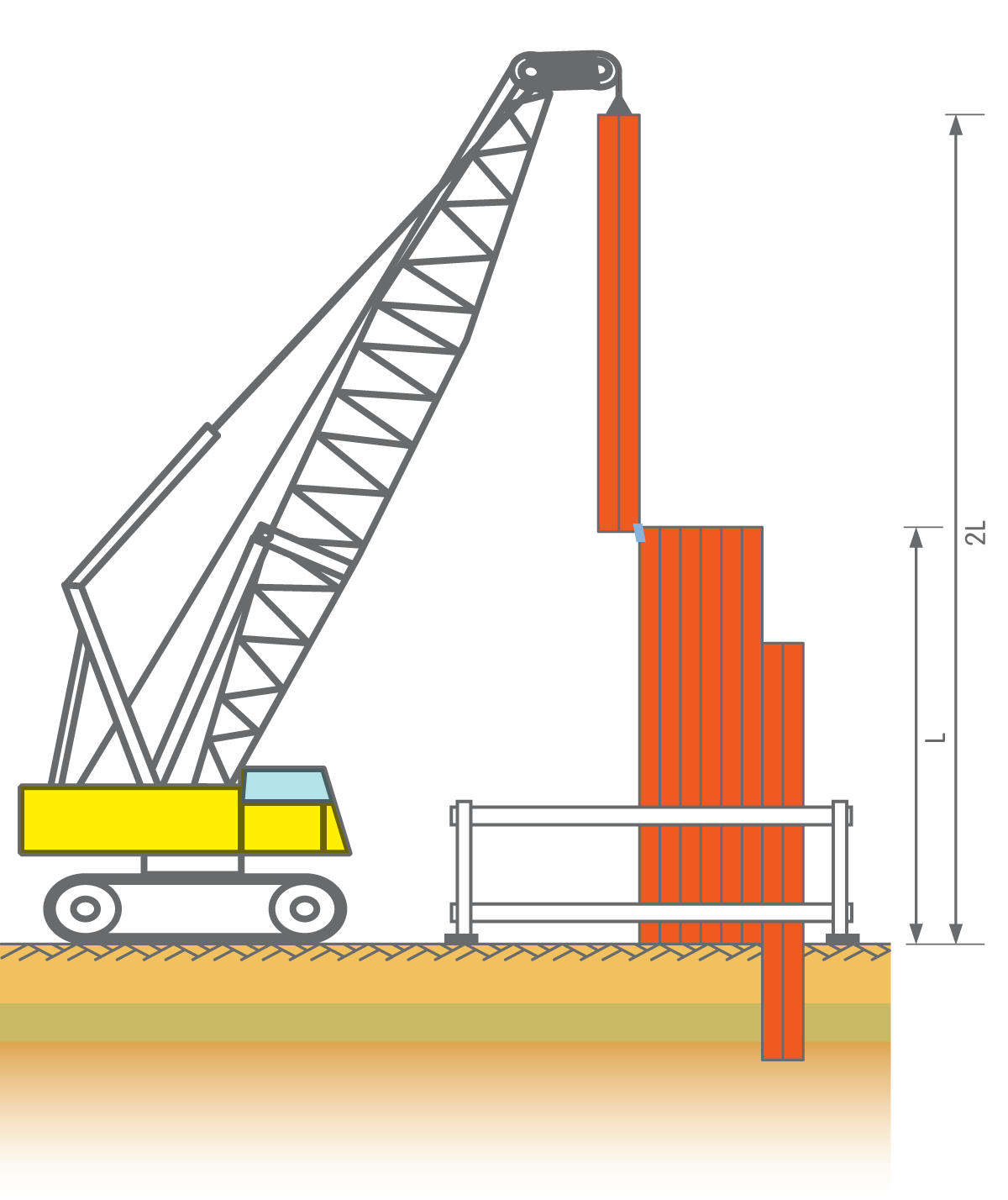
Picture 1: threading of steel sheet piles into a panel
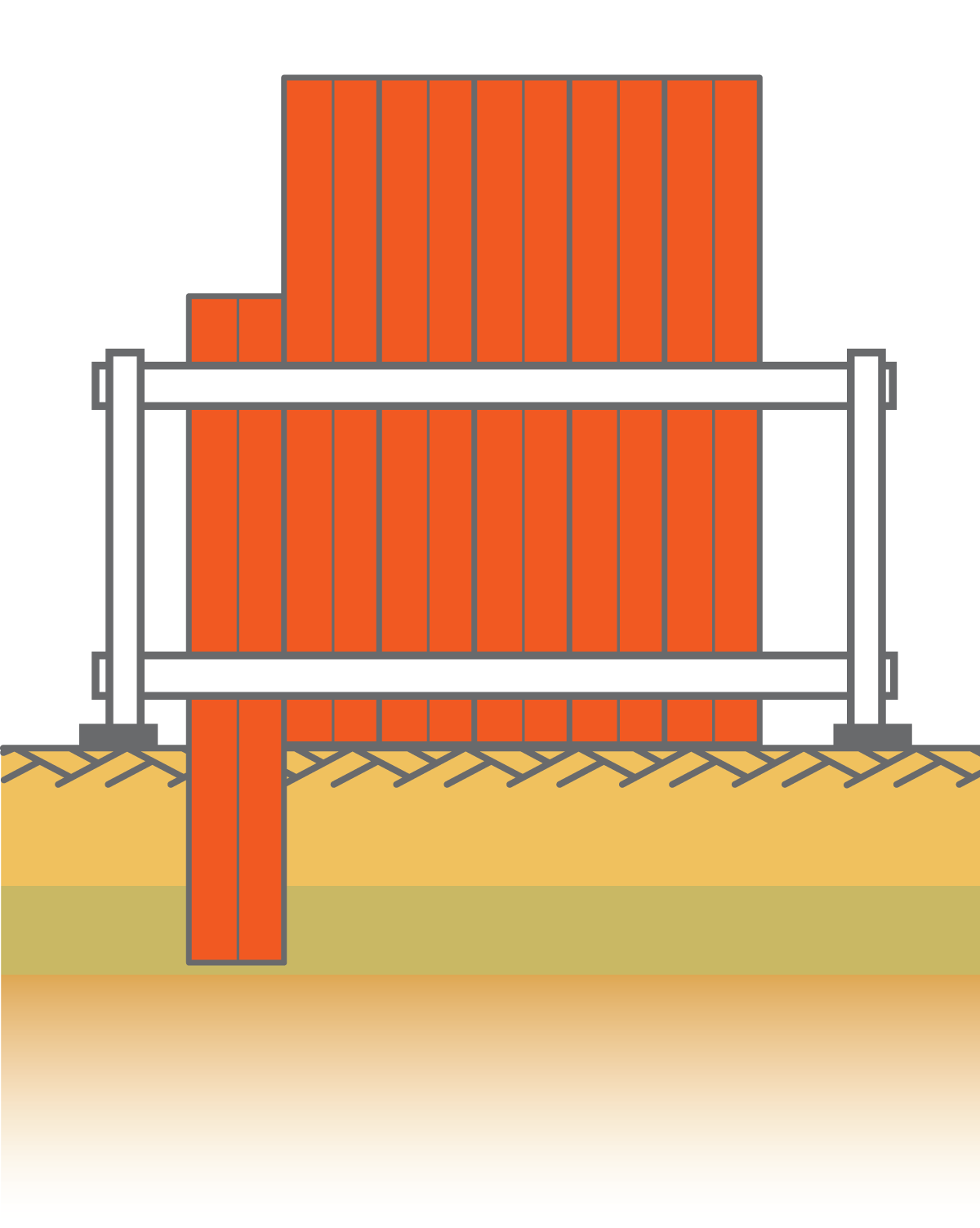
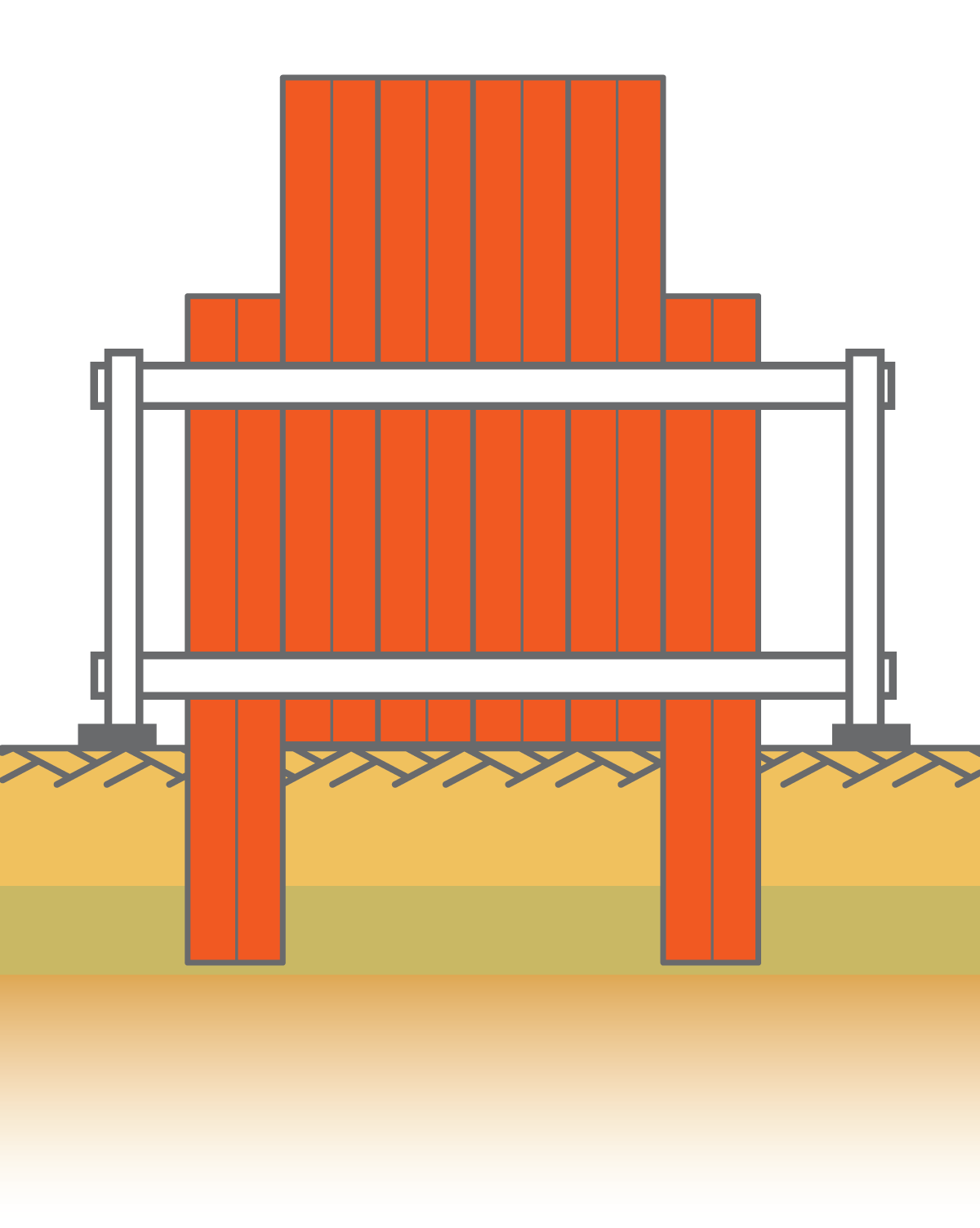
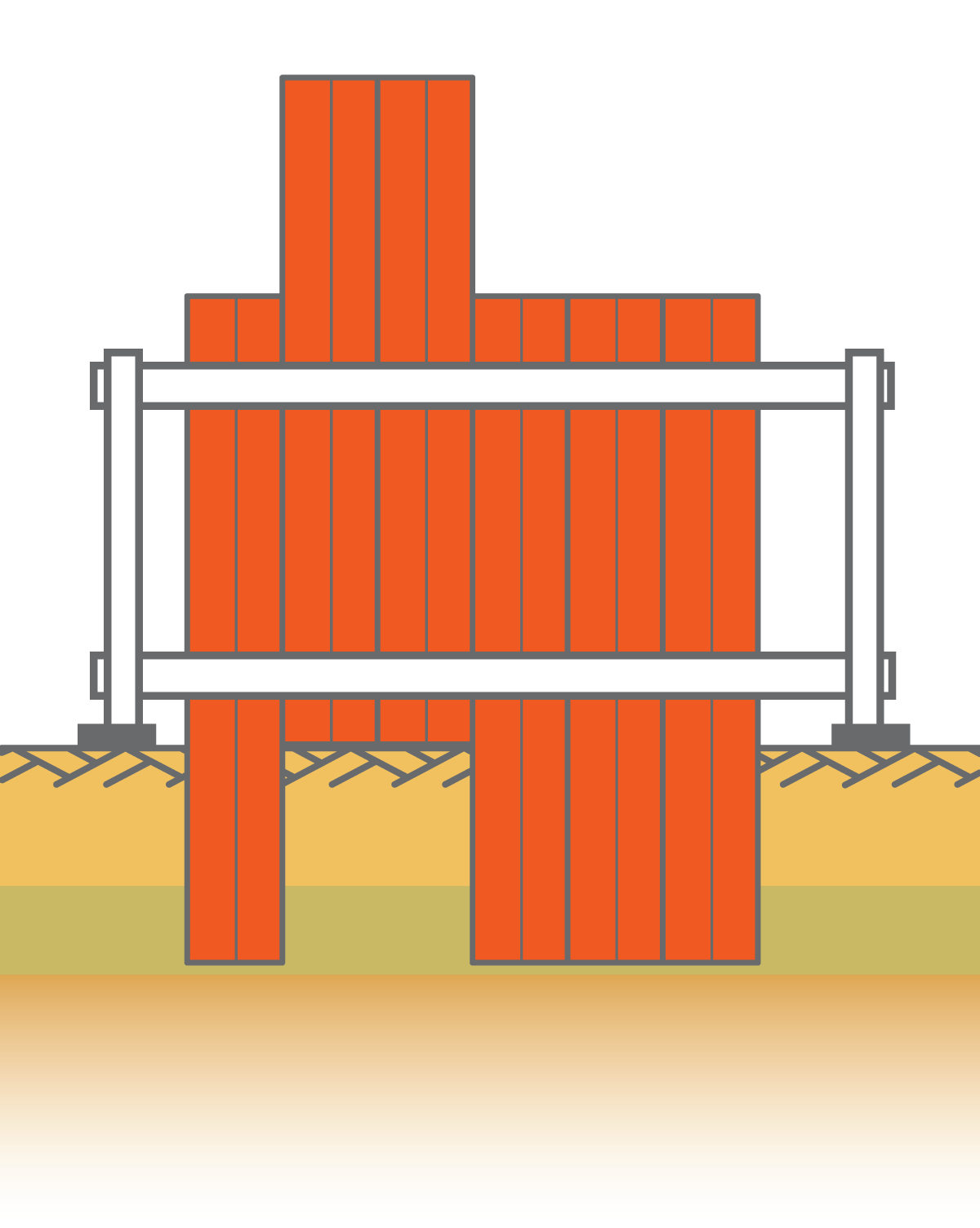
Picture 2: panel driving sequence
Panel driving combined with staggered driving
There are two methods. The concept is identical to the previous one, with the exception of the staggering of the sheet piles driven.In very compact soils, reinforcing the tips of some of the piles improves the performance, but usually, only every other pile is reinforced, so that the non-reinforced piles (2 and 4 in the picture below) shall never be driven deeper than the reinforced ones.
Main advantage: better performance in very compact soils.
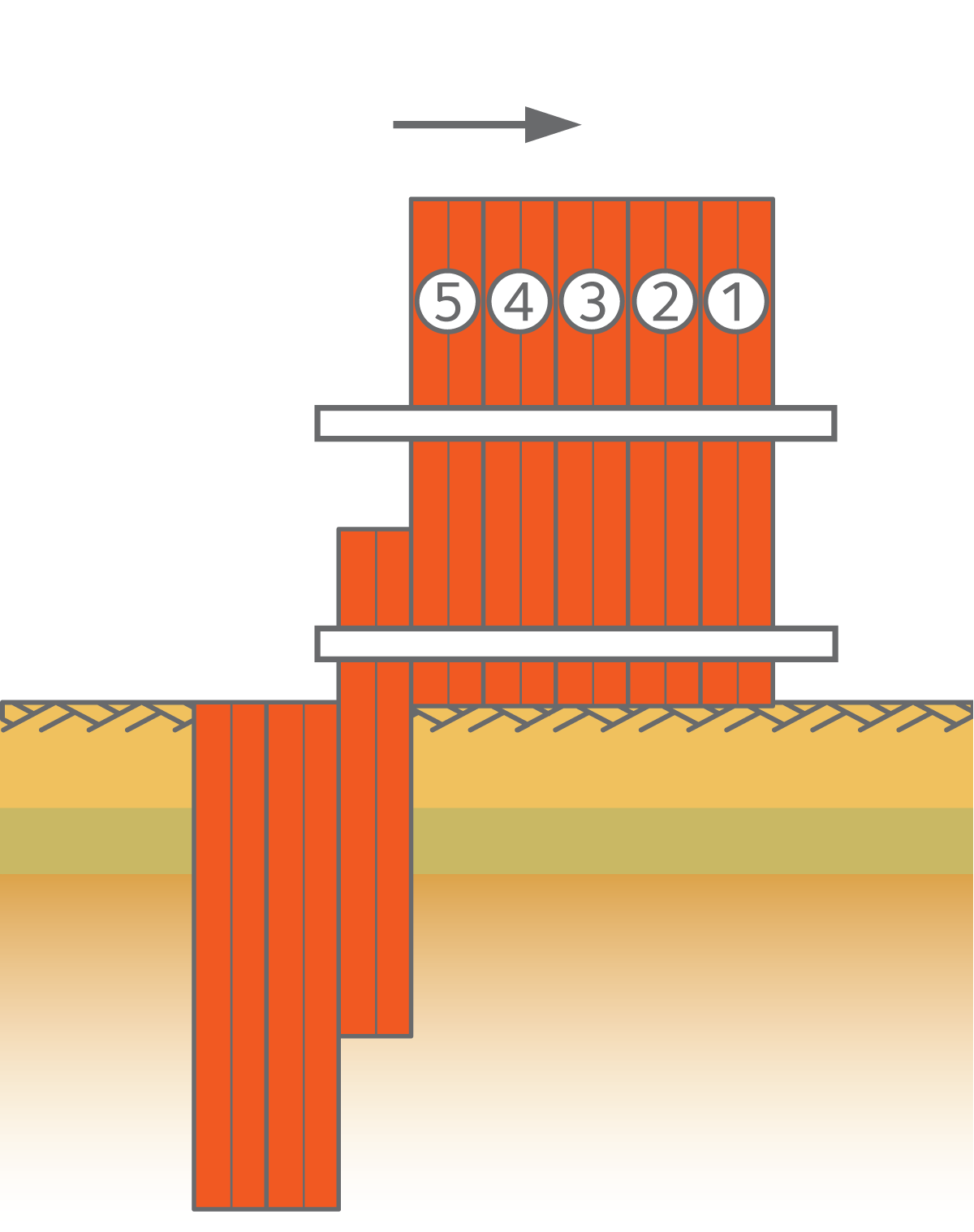

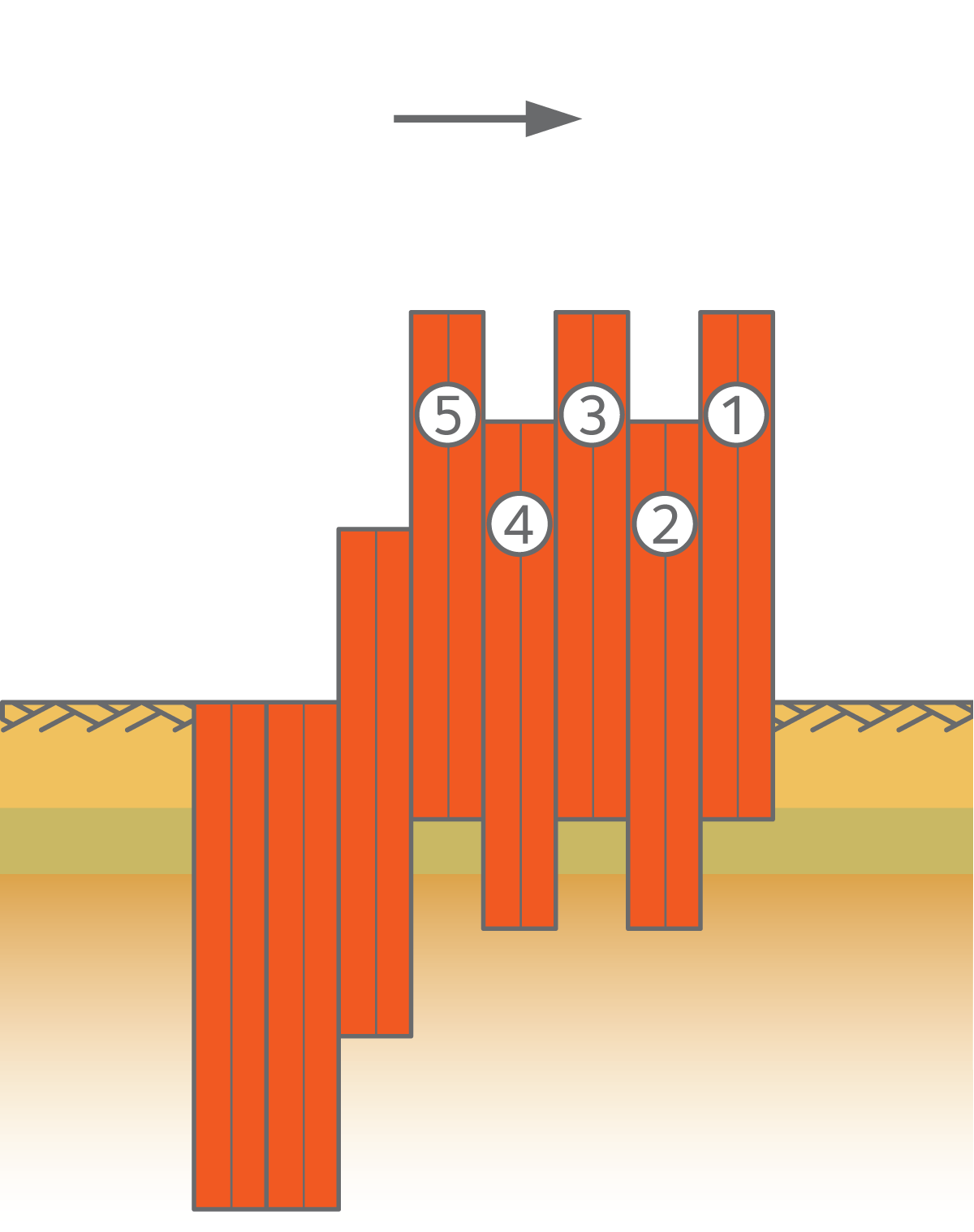
Picture 3: panel driving combined with staggered driving
Pitch and drive
The concept is very simple: each sheet pile is threaded and driven directly to its final depth. Hence, it is quite fast, and cheap. It can be suitable when- tight installation tolerances are not a major concern (mainly for temporary walls),
- sheet pile are quite short,
- leaning is not a predictable issue,
- soil layers are not too compact,
- ...
Driving assistance
Driving assistance should be considered in cases where it is not possible to use heavy equipment, or to reduce vibrations and noise, and in very compact soils:- waterjetting,
- pre-drilling or pre-augering,
- blasting.
Pre-drilling reduces also the resistance of the soil. The location of the drills is of utmost importance and should be determined by experienced professionals.
Note that some local regulations impose a reduction on the bearing capacity of soils loosened with waterjetting or pre-drilling / pre-augering.
You can find many more details about installation methods in the Piling Handbook and in the Installation manual.
Dernière modification : novembre 11, 2024